

In this third article of a four-part series, researchers from Michigan State University share science-based information about indoor production of leafy greens and herbs. To read part one, click here. To read part two, click here.
In recent years, researchers and growers have been mainly focused on quantifying the effects of sole-source light quality on crops grown in indoor CEA warehouses and containers. However, one commonly overlooked environmental parameter that has the potential to increase growth and yield is carbon dioxide (CO2). Atmospheric (ambient) CO2 concentration has been increasing over the years from below 320 µmol·mol-1 (or parts per million, ppm) in 1960 to current values where CO2 levels outdoors comprise 0.04% of atmospheric volume, or around 400 µmol·mol-1. However, CO2 concentrations in a “tightly sealed” greenhouse or indoor growing operation can quickly dip down to 200 µmol·mol-1 as plants use CO2 during photosynthesis. You may think that maintaining the CO2 concentration at ambient levels is as easy as venting or introducing fresh air. It can be during certain times of the year, but this can be difficult when outdoor temperatures are very low. Increasing CO2 to concentrations above ambient and up to 1,200 µmol·mol-1 has been shown to increase photosynthetic rates, growth and yield. There are several commercial methods to increase CO2 concentrations above atmospheric levels. However, these methods should be deployed during periods when ventilation is minimal to reduce the loss of the added CO2 outside of the growing area.
For CO2 enrichment above ambient, growers can deploy CO2 burners that produce CO2. This method produces some heat, moisture and CO2 by burning natural gas or propane. Incomplete combustion or contaminated fuels can lead to the introduction of toxic gases for both plants and humans. To improve CO2 uniformity, burners should be dispersed throughout and horizontal air flow (HAF) fans can be deployed to circulate air. Another method of CO2 enrichment for both greenhouses and indoor farms is injecting compressed or liquid CO2 from a tank. The compressed CO2 is converted from a liquid to a gas and then released into the growing area. These tanks can be rented or purchased through local gas distributors. When delivered in this form, CO2 is often dispersed through polyethylene tubes. Remember that CO2 is heavier than the other air components, so concentrations tend to be greater closer to the floor.



Experimental protocol
The goal of our research program is to develop indoor and greenhouse environmental management protocols for different stages of culinary herb production. Given that CEA production is energy-intensive, we have focused our efforts on young plant production since inputs such as light and CO2 can be delivered across more plants at the seedling stage when plant density is greater compared to the finished stage when plant density is lower. The objectives of our research were to determine if indoor CO2 enrichment during the seedling stage influences: 1) sweet basil seedling growth and development; 2) morphology, growth, and yield at harvest in the greenhouse; and 3) volatile oil content and flavor (this research is in progress and we will report the results in an upcoming article).
Sweet basil ‘Nufar’ seeds were sown in Grodan rock-wool cubes and placed in walk-in growth chambers with an average daily temperature (ADT) set point of 73° F (23° C) and CO2 set points of 500 or 1,000 µmol·mol-1 throughout the day and night. We maintained these concentrations by injecting compressed CO2 into the chambers, and by scrubbing CO2 with soda lime when concentrations were too high. In each chamber we had four light intensity treatments of 100, 200, 400 and 600 µmol·m–2·s–1 that operated 16 h per day to create daily light integrals (DLIs) of 6, 12, 23 or 35 mol·m–2·s–1. This allowed us to determine whether there was an interaction between CO2 concentration and light intensity. The seedlings were grown for two weeks, after which plants were transplanted into deep flow technique (DFT) hydroponic systems in a greenhouse with an ADT of 73° F (23° C) and a DLI of 14 mol·m–2·s–1. With the plants growing in a common greenhouse environment, we could evaluate if differences or higher inputs at the seedling stage would result in increased yields down the road.
In theory, by increasing CO2 concentration, we should have seen increased growth; however, this was not the case. As can be seen in Figs. 1 and 2, light intensity had a much larger impact on seedling growth than CO2, but we will discuss that in the next article of this series. Increasing CO2 concentration did not influence growth and development. Why would increasing CO2 from 500 to 1,000 µmol·mol-1 not actually improve growth and development of basil seedlings?

There are three main limitations to photosynthesis: the supply or utilization of CO2, of light, or of phosphate (also referred to as biochemical limitation; Fig 3.). Theoretically, if CO2 concentration starts at 0 and increases, you will hit a CO2 compensation point above which plants have positive net photosynthesis. As the CO2 concentration further increases, the photosynthetic rate will increase until the CO2 concentration reaches a species or cultivar-dependent saturation point. In our case, 500 µmol·mol-1 CO2 may have been near the saturation point for basil seedlings. Therefore, increasing the concentration to 1,000 µmol·mol-1 did not significantly increase growth. In addition, if photosynthesis is light-limited, increasing CO2 concentration will not result in large increases in photosynthesis. Conversely, if photosynthesis is CO2-limited, increasing light intensity will not result in large increases in photosynthesis. However, increasing CO2 can have some other positive effects, including reducing oxygenation and photorespiration. In our case, increasing the light intensity further or growing the plants past the transplant stage may have resulted in differences between CO2 treatments.
Do our results mean we should write off CO2 enrichment as a means of increasing photosynthesis and ultimately growth and yield? No. We are currently evaluating several other culinary herbs at lower and higher CO2 concentrations and a range of light intensities to see if there is a species-dependent response. In addition, it is possible that elevating CO2 concentration would have a larger impact during the finish stage. More studies are needed to parse out which horticultural crops and at what stage of production CO2 enrichment would be the most beneficial to improving growth and yield.
Take-home message
Other environmental factors besides CO2 concentration may have a larger impact during the seedling stage. Read the last article in this four-part series to understand the benefits of increasing indoor CEA light intensity during propagation on subsequent yield in the greenhouse.
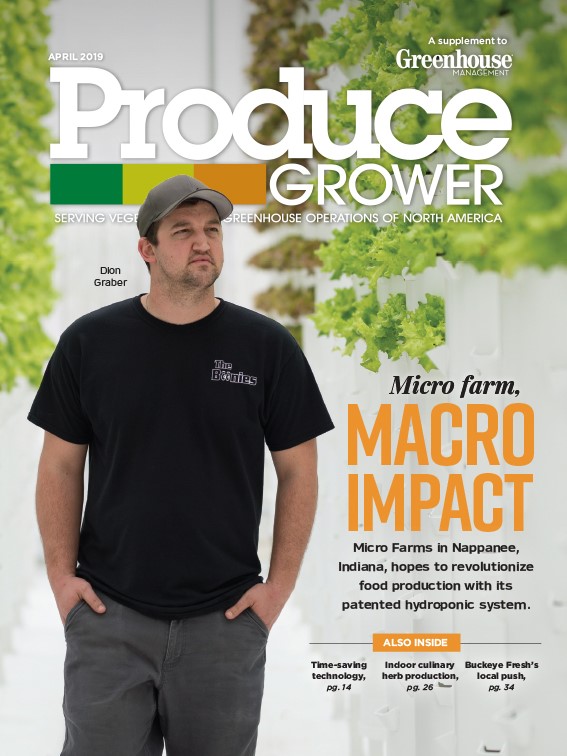
Explore the April 2019 Issue
Check out more from this issue and find your next story to read.
Latest from Produce Grower
- Chilli thrips (Scirtothrips dorsalis)
- GS1 US Celebrates 50-Year Barcode 'Scanniversary' and Heralds Next-Generation Barcode to Support Modern Commerce
- University of Florida offers Greenhouse Training Online program on irrigation water
- Flower trends in full bloom
- Nominate an outstanding leader
- New Florida Extension Agent Will Teach Stakeholders About Food Safety
- Paint it black
- Regular checkups